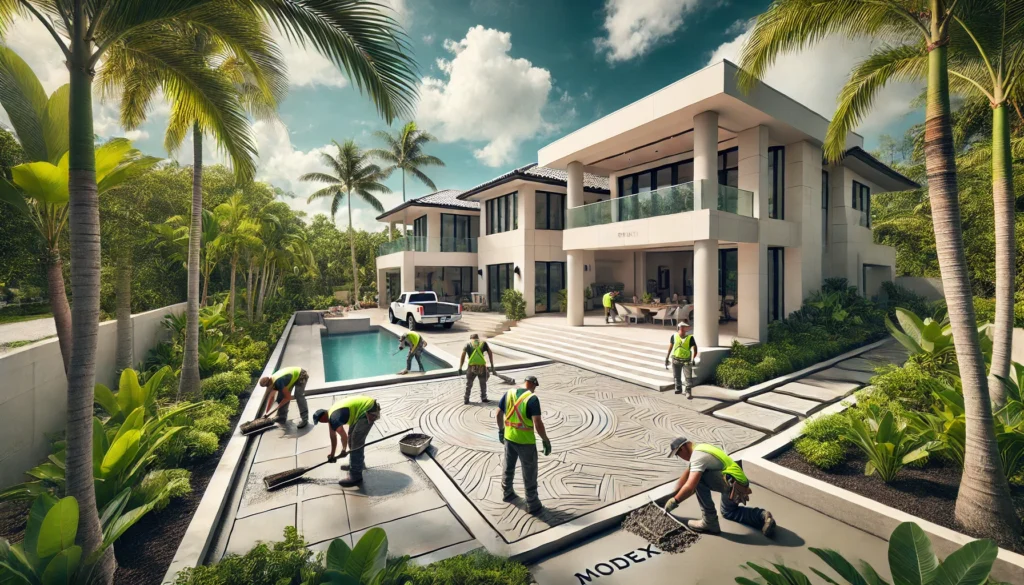
At Modex Stamped Concrete Miami, we specialize in transforming ordinary surfaces into stunning, textured artwork through our expert stamped concrete installation services. Using high-quality materials and innovative techniques, our skilled team creates beautiful patterns and designs that mimic natural stone, brick, or tile, enhancing the aesthetic appeal of patios, driveways, walkways, and pool decks. Whether you’re looking to add a touch of sophistication to your outdoor space or improve your property’s curb appeal, we work closely with you to customize each project, ensuring that it aligns perfectly with your vision and complements your home’s architecture. With our commitment to durability and excellence, you can trust Modex Stamped Concrete Miami to deliver impressive results that stand the test of time.
Preparing Your Site for Installation
Proper site preparation is crucial for the success of your stamped concrete project. Begin by assessing the area where the installation will take place. Ensure the surface is level and clear of any debris, vegetation, or old concrete that might interfere with the new slab. If you are working with a patio or driveway, it is important to evaluate the subgrade for stability. Any necessary reinforcement, like rebar or mesh, should be included to enhance the durability of the concrete.
Next, establish the proper drainage to prevent moisture accumulation, which could damage the stamped surface over time. Create a slight slope away from structures to direct water flow. Once the groundwork is laid, use a foam or lumber form to outline the perimeter of the area, ensuring it is well-secured and holds the desired shape. Pay close attention to any additional features you might want, such as bullnose edges for walkways or steps, and ensure they are integrated into your plans before moving on to the actual pouring and stamping process.
Essential Preparation Steps
A solid foundation is crucial for any successful stamped concrete installation. Begin by assessing the site for soil quality and density. Make sure to clear away any existing debris, vegetation, or boulders that may interfere with the installation. If the ground is uneven, utilize a grading shovel or a compactor to level it out. A well-prepared subbase usually consists of gravel or sand, which allows for proper drainage and reduces potential stress on the surface once cured.
Once the area is prepared, measure and mark the layout with stakes and a string line to guide the installation. It is essential to consider weather conditions, as extreme temperatures can affect the curing process. If rain is forecasted, plan accordingly to protect the newly poured concrete. During installation, use a screed to ensure the concrete is even and consistently thick across the surface. Remember to install expansion joints to allow for movement, which will help maintain the structural integrity of the patio over time.
Maintenance Tips for Stamped Surfaces
Maintaining stamped surfaces requires a thoughtful approach to ensure their longevity and aesthetic appeal. Regular cleaning plays a crucial role; using a power washer can effectively remove debris without damaging the surface. It’s essential to avoid harsh chemicals that might strip the protective sealant. Instead, a mild detergent mixed with water works well. After cleaning, inspect the surface for any signs of wear or damage. Touching up the coating may be necessary to protect against moisture or staining.
Applying a protective sealant every few years can greatly enhance the surface’s durability and resistance to the elements. Ensure the surface is dry prior to application for optimal results. A quality acrylic or epoxy sealant can help shield against fading and deterioration from UV exposure. Be mindful of the weather conditions during application to achieve the best bonding. Regular inspections and maintenance will keep your stamped concrete looking vibrant and fresh for years to come.
Keeping Your Patio in Top Condition
Proper upkeep of stamped concrete is essential for prolonging its lifespan and maintaining its aesthetic appeal. Regularly cleaning the surface with a power washer can help remove dirt and debris that can degrade the finish. Using a mild detergent can enhance the cleaning process without damaging the color. Always ensure that the sealed surface doesn’t accumulate moisture, as this can lead to deterioration over time. For added protection, consider applying a fresh coat of sealant every couple of years to reinforce the existing layer and improve resistance against stains and abrasion.
Monitoring for cracks or chips should be a part of any maintenance plan. Repairing these imperfections promptly will prevent them from widening and becoming more costly to fix. When resurfacing, make sure to choose a quality product that is compatible with your existing structure and color. During extreme temperature conditions, such as significant heat or cold, avoid heavy foot traffic to minimize stress on the material. This vigilance will aid in preserving the integrity and appearance of your outdoor spaces, whether it’s a patio, porch, or deck.
Common Mistakes to Avoid
One prevalent mistake during installation is inadequate preparation of the site. Failing to inspect and address issues such as soil erosion or uneven ground can lead to future problems, including cracking and water damage. Properly tamping the soil and using plywood or styrofoam as support can enhance the structural integrity of the project. Ignoring proper measurements during this phase can also result in misaligned patterns or uneven surfaces, diminishing the overall appearance of the stamped concrete.
Another common pitfall involves the choice of materials and techniques used in the installation process. Relying solely on low-quality brands for aggregates or sealants can lead to issues like efflorescence or reduced durability. It is essential to research different options and choose products designed specifically for stamped concrete applications. Mixing concrete improperly can result in weakened sections, while neglecting to add polypropylene fibers may increase the risk of shrinkage cracking. Ensuring proper formwork and taking time to follow best practices significantly impacts the final outcome.
Pitfalls During Installation
One common issue during installation arises from inadequate site preparation. Failing to properly assess the landscape can lead to complications like water pooling, which may damage the stamped surfaces over time. Ensuring that the ground is level and that any existing debris is cleared away is essential for achieving the desired aesthetic. Attention to detail in the initial stages minimizes the risk of future problems.
Another significant pitfall involves using the wrong materials or tools, which can compromise the overall quality. For instance, not selecting appropriate sealants or cement mixtures may affect adhesion and durability. Utilizing incompatible powders or primers can lead to an uneven finish or colour discrepancies. Proper research and adherence to manufacturer guidelines enhance the longevity and appearance of the finished product.
FAQS
What is stamped concrete?
Stamped concrete is a decorative form of concrete that replicates the appearance of natural stone, brick, or other materials using molds and color additives.
How long does the installation process take?
The installation process for stamped concrete typically takes one to three days, depending on the size and complexity of the project. Curing time may take an additional week.
Can I install stamped concrete myself?
While it’s possible to install stamped concrete yourself, it requires a good understanding of concrete work and access to specialized tools. Hiring a professional is often recommended for the best results.
How do I maintain my stamped concrete surface?
Regular maintenance for stamped concrete includes cleaning with mild soap and water, sealing the surface every one to three years, and promptly addressing any cracks or damage.
What are some common mistakes to avoid during stamped concrete installation?
Common mistakes include poor site preparation, inadequate mixing of concrete, not using enough color hardener, neglecting to seal the surface, and rushing the curing process.
Served areas in Miami:
Bay Heights
Allapattah
Bayshore
Brickell Hammock
Buena Vista
Coconut Grove
Dinner Key
Edison Center
Fronton Trailer Park
HMS Bounty
Latin Quarter
Liberty Square
Little Haiti
Little Havana
Little River
Ocean View Heights
Royal Duke Trailer Court
Sabal Palm Plaza
Shenandoah
Silver Bluff Estates
Silver Court Trailer Park
South Bay Estates
The Pines
The Roads
Torch of Friendship
Wynwood